Affordable but
most advanced engineering solutions………
Click Here For Video
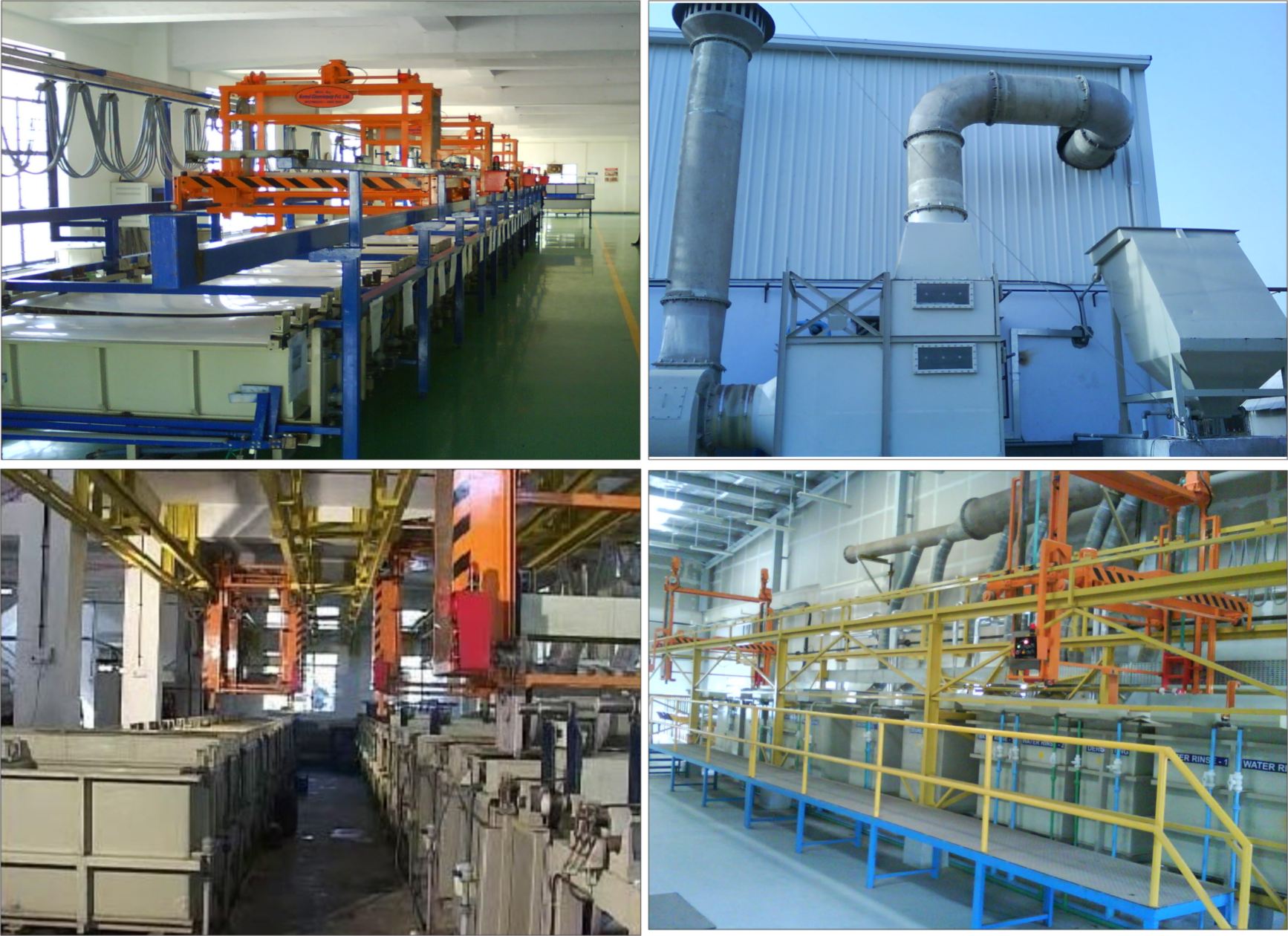
Plants (Process
Tank & Ancilliaries, Flight Bars, Transporters, PLC,
Control Panel, Exhaust, ETP, Structure etc) *
Planning * Installation, * Commissioning,
*Maintenance, * After Sales Service backup
Fully
Automatic Plating Plants are used in the metal finishing
industry to carry components held commonly in Racks or
Barrel, mechanically through a number of treatment cycle
Tanks, by means of PLC operated transport wagons.
The
advantages of "KCPL" Automatic plants are direct savings
in labour cost, Better process application & production
control, Improved solution maintenance and quality control,
Lower floor space, Possibility of larger and deeper Tanks
with larger and heavier rack sizes. Better control of
dragout, Lesser danger of solution contamination, Efficient
fume extraction and ventilation, High quality ETP process
and so on……all leading to a high rate of economy in production
costing.
KCPL plating
and metal finishing plant includes manufacturing of complete
Plant such as Process Tanks & Ancillaries, Flight
Bars, Material Handling Systems, PLC Automation, Centralised
Control Panel, Fume Exhaust System, Heating System, Cooling
System, Effluent Treatment Plant, Service line connection,
etc. * Installation * Commissioning * Maintenance * After
Sales Service backup. We can undertake complete responsibility
for all peripheral aspects of an automatic plant as featured
above including training of operated personnel. We have
our own specialist staff for installing the plant and
equipment so as to enable smooth, dependable and successful
commissioning with our responsibility.
Why
opt for Komal Automatic Systems?
1) Use
less floor space (generally this is true only when production
levels are considered with labour involved). Depending
on the transfer mechanism used, more floor space may be
required, but will deliver higher production at lower
unit labour cost.
2) Larger and deeper tanks are possible.
3) Larger and heavier rack sizes are possible.
4) Better control of dragout. This is mainly the result
of controlled transfer time, and also provides better
and more complete drainage between tanks.
5) Less danger of solution contamination.
6) Better rack life and control of insulation of contacts.
This depends on the Komal loading and unloading procedures
used.
7) More efficient ventilation is possible.
8) Lower installation cost. Depends on the equipment selected,
modified by labour savings.
9) Better process control. A function of controlled processing
times.
10) Better production control.
11) Less costly and improved solution maintenance.
12) Better control of quality and specifications.
13) Lower rejects.
14) More efficient use of labour and materials.
15) Improved working environment.
As
a buyer, what are the factors you must consider while
selecting a fully automatic machine?
1. Production
requirements
2. Specification
3. Work load and rack size or Barrel Size / Capacity
4. Carrier spacing
5. Number of lanes
6. Treatment cycles
7. Load output / hour
8. Transfer time
9. Anode rod spacing
10. Current requirements per load
KCPL
has a range of Metal Finishing Systems, Plants & Equipments
for:
• Electroplating
• Electrolytic and Electroless Plating
• Phosphating
• Anodising
• Electrophoretic Coating
• Electropolishing
• Chromating
• Cleaning
• Pickling
• Effluent Treatment Plant (Waste Treatment Plant)
• Fume Exhaust Systems (Ventilation Systems)
• Water Purification Systems
• Special Purpouse Machinery
• Filteration Systems
Whether
modifying / upgrading an existing plating systems or designing,
manufacturing and installing a new automatic / manual
line, our inhouse machinery, assembly, electrical, piping,
sandblasting, polishing, painting and plastisol coating
offers premium quality, economy and speed of execution,
backed by one of the industry's best and qualified Technical
(Design & Engineering), Quality, Manufacturing and
support staff.
Electroplating
Systems for Mild Steel, Stainless Steel, Copper, Aluminium,
Plastic: side arm machines, split rails, overhead hoist,
barrel plating lines for:-
• ENP Systems
• Copper Plating Equipment
• Chrome Plating Equipment
• Nickel Plating Equipment
• Nickel Chrome Plating System
• Brass Plating Equipment
• Precious Metal Plating System
• Zinc Plating System
• Tin Plating System
• Tin Zinc Plating System
• Plating on Plastic: Decorative Chrome, others
• Phosphating System
• Anodizing System
• Blackodizing System
• Chromatizing System
KCPL's array of Electroplating System
Rack (Vat) Plating Plants
for Metal or Plating on Plastic with modular design and
high capacity with fixed, flexible-fixed or random timeways.
Barrel Plating for Metals,
ideal for small or difficult to handle parts, with high
capacity, automatic loading / unloading.
Split Rail Return Type
Rack processing for Metal with automatic operation. Ideal
for fixed cycle work at high throughput.
Komal also supplies with
the above systems a complete range of material handling
( vibratory feeders, chutes and powered part movers) and
auxiliary equipment including dryer, chemical dosing,
filtration and chemical recovery, fume exhaust system,
Centrifugal fan, Mist Eliminators, exhaust hoods, duct,
fume scrubbers, Effluent Treatment Plant (ETP, Waste Water
System), Clarifier, Scrubber, as part of the complete
system.
KCPL's
Decorative Plating Equipment Systems
Manual and Automatic processing equipment systems for
plating Aluminium, Copper, Brass, Steel and Stainless
Steel parts with Copper, Nickel, Chrome, Brass, Silver,
Gold, Tin, Lead and others.
KCPL's
Industrial Plating Equipment System
Manual and Automatic processing systems for plating Aluminium,
Copper, Brass, Steel and Stainless Steel parts with Cadmium,
Hard Chrome, Tin, Lead, Nickel and Zinc, Silver, Gold,
CED coatings.
KCPL's
Aircraft Plating Equipment
Large tank system specifically designed from Hard Chrome,
Nickel and Cadmium plating of extraordinary size and aircraft
parts.
KCPL's
Anodizing Equipment System
Manual and Automating process equipment systems for Anodizing
type I, II hardcoating of Aluminium parts.
KCPL's
range of Anodise Systems
Type I CAA - Chromic Acid Anodized
Type II SAA - Sulphuric Acid Anodize
Type III HAA - Hardcoat Acid Anodize
PAA - Phosphoric Acid Anodize
BSAA - Boric Sulfuric Anodize
KCPL's Conversion Coating
Phosphating
Chromatizing
Blackodising
KCPL's
Electropolishing Equipment System
Manual and semi automatic straight line processing equipment
system of Electropolishing of Stainless Steel and Alumnium
parts.
The above systems include
Process and rinse tanks, rectifiers and bus work, temperature
control, solution agitation, hoists, ventilation hoods,
fume scrubber, electrical control panels, and all electrical
and plumbing interconnecting between related components.
KCPL's Manual Plating Lines
The Manual Plating design
is based on the modular type tanks, heater, thermostats,
exhaust hoods, incoming plumbing, drain plumbing, drain
plumbing, etc into one integral system. It is manufactured
in sections making it easy to manipulate and install.
Key
features of this Manual system are:
Rugged construction
The modular system is constructed from 8-15mm polypropylene
sheet with encapsulated steel located in critical areas,
to prevent distortion.
Installation
The system is designed to keep your installation time
and materials at a minimum. All electrical controls are
prewired to the front control console, all drains and
incoming plumbing are pre-plumbed to termination and inlet
points, the exhaust hood/ plenum system is an integral
part of the module. All are designed for simple and inexpensive
installations.
Quality
Raw material and electrical component are selected based
on reliability.
Maintenance
The systems are designed for maximum accessibility to
all components with smooth, unobstructed surface areas
which are easy to clean.
KCPL's
Turnkey Metal Finishing Systems
KCPL's speciality…starting
with an empty floor, our engineers work sytematically
with our
customers to develop a basic floor plan for their metal
finishing system. Process system. Process
tanks are then designed to meet the criteria of our customers
based on chemical content,
temperature and the size of the parts being processed.
Once that has been accomplished, tanks
are laid out on the floor plan in our CAD department and
a picture of the metal finishing shop
starts to take form.
Chemical containment
curb are designed, material handling system, ventilation,
waste treatment
systems, grating system, heating and chilling equipment,
automatic water replenishment,
filtration systems, and any other options our customer
desires are also laid out. The custom
equipment is then manufactured, and the equipment is moved
into place. Utilities are hooked
up, chemicals are added and with the permission of the
municipalities, our customer is up and
running with their brand new, custom designed Metal Finishing
System.
LAYOUTS
Generally
as shown in the plans below. Similarly 'L' or Round shaped
plant layouts are designed depending on the requirements.
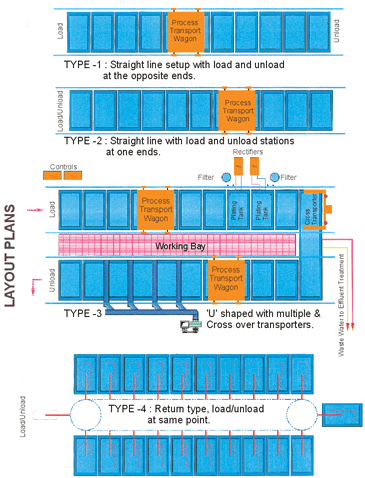